Jedes Koordinatensystem hat einen Ursprung, den Nullpunkt. Bei der CNC Arbeit gibt es gleich mehrere Nullpunkte. Die verschiedenen Nullpunkte dürfen nicht verwechselt werden. Hier zunächst eine Beschreibung für den wichtigsten CNC-Nullpunkt.
Der Programm-Nullpunkt ist der Ursprung des NC-Codes.
Bei CNC-Programmieren wird der Nullpunkt, das ist wichtig, vor Beginn der Programmierung im CAM-Programm festgelegt. Überlegen Sie vorher wie Sie der Nullpunkt später am Rohteil festzulegen ist.
Ist der NC-Code fertig und zur Maschine übergeben, kann das Rohteil aufgespannt und dort der Nullpunkt am Rohteil entsprechend festgelegt werden. Dann spricht man auch vom Werkstück-Nullpunkt. Das CNC-Programm läuft nun an der richtigen Stelle, nämlich da wo das Rohteil ist,
Programm-Nullpunkt = Werkstück-Nullpunkt
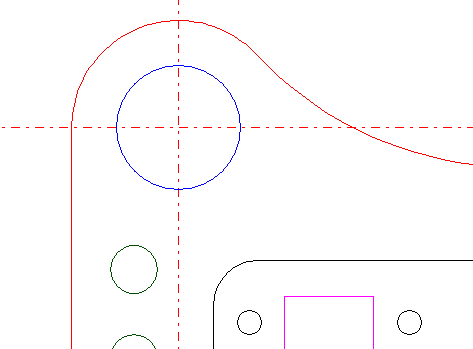
Ob der Programm-Nullpunkt in der Mitte desTeils, an einer Ecke oder an einem speziell Punkt richtet sich danach wie einfach sich der Werkstück-Nullpunkt Einstellen lässt. Wichtig ist das Werkstück- und Programm-Nullpunkt an der gleichen Stelle des Rohteils bzw. der Geometrie festgelegt werden.
So legen Sie den Werkstück-Nullpunkt fest.
An der CNC Steuerung kann der Werkstück-Nullpunkt meist für jede Achse einzeln gespeichert werden. Oder er wird für die X und Y-Achse gemeinsam festgelegt. Fahren Sie das Werkzeug an den gewünschten X-Y Nullpunkt und speichern diese Stelle ab.
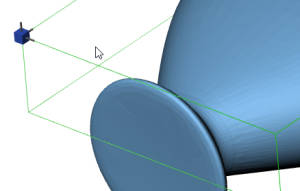
Bei der Z-Achse (senkrechte Achse) wird meist anders verfahren. Im Normalfall ist der „Z-Werkstück-Nullpunkt“ immer auf der „Oberkante des Teils“ bzw. etwas darunter oder auf die „Tisch-Oberfläche“ (Teil Unterkante). Das wird je nach Branchen unterschiedlich gehandelt. Im Maschinenbau wird meistens die Oberkante des Teils, bei der Holzbearbeitung meist die Unterkante (Oberkante Tisch) benutzt weil oft gleiche Plattenstärken verarbeitet werden. Fräswege vom Nullpunkt aus nach unten sind meist mit einem Minuszeichen einzugeben. Einige CNC-Steuerungen haben je nach Einsatzfall auch andere Einstellungen.
Soll der Werkstück-Nullpunkt auf der Oberkante des Rohteils liegen, wird die Maschine bei der Einstellung des Z-Werkstück-Nullpunktes mit der Hand-Steuerung so gefahren das das Werkzeug die Oberfläche leicht ankratzt. Am besten an einer Stelle wo sich nach der Bearbeitung kein Material mehr befindet.
Die Z-Koordinaten im CNC-Programm beziehen sich immer auf die Werkzeugspitze.
Das bedeutet das nach einem Werkzeugwechsel der Z-Nullpunkt neu eingestellt werden muss. Man sagt dazu auch das Werkzeug wird „genullt“.
Bei Maschinen mit einem automatischen Werkzeugwechsler werden die Werkzeuge vorher „genullt“.